Introduction: Stack molding is a a high production, sand casting, or green sand molding process. The piston ring people know this method well. Simply explained, the bottom of a given flask in a stack provides the cope of the flask below, while the top, provides the drag of the next layer�"pan caked- casting ".
Process: Ina stack mold the two mold parting surfaces or mold split lines. A stack mold does not require much more clamp force than a single phase mold because the projected part surface areas of the cavities on both sides of the center block cancel out each others force. A rule of thumb for a clamp force estimate is to take the projected part surface area times the melt pressure and multiply it by a factor of 1.1.
Without increasing the machine platen size you can double the amount of cavities producing parts. Most stack molds have an equal number of the same cavities in each parting surface. For example, a 2+2 cavity grid mold with an 8+8 hotrunner produces four identical parts per cycle. Some stack molds have different cavities in each mold parting surface and they produce a family of parts per shot, each different in shape and size (such as this collapsible crate). The floor and four side walls of this collapsible crate are produced in one shot. Fill, pack, cool and warp analysis accurately simulate the flow of the melt during the design phase of a project. This optimizes plastic part quality and the production output by improving cycle time.
Some stack molds can also handle multi-material injection, different materials such as hard/soft combination or multi-color molding. Three level stack molds are not as common as two level stack molds.
When the stack mold opens for the ejection of parts, both mold parting surfaces open (in most cases simultaneously) by means of a mechanical connection between the mold cente
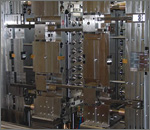
r block, the fixed halves of the mold and the moving half of the mold. The mechanical connection which moves the center block of the mold can be:
- A rack and gear operated motion system
- A harmonic lever system
- A hydraulic push-pull systems or
- A helical gear system
Aside from the center block motion system, another key element of a stack mold is the hotrunner system. The transfer of plastic melt from the machine barrel into the mold center block has traditionally been achieved by a heated sprue bar which leads the melt from the machine nozzle through the fixed mold half and through the first mold parting surface into the hotrunner manifold, which is located in the center block of the stack mold.
Application: Piston rings
Advantages:
- Decreases number of machines required
- Lower machine size requirement vs.. multi-cavity single face molds
- Produce twice as many parts without increasing press size or clamp tonnage, which greatly reduces part costs
- Set-up time and run-time costs are divided by all the parts produced
- Producing the front and back parts of a key fob at the same time is a good example of an application for stack molding.