Introduction: The process of molding two or more materials in the same cavity in the same shot, by a combination of transfer and compression molding.
Process: A master male pattern is made. The master can be made from any material that can tolerate epoxy, such as foam or wood. However, typically the master pattern is a stereolithography part. An RTV mold is made of the master pattern and a urethane male pattern is made from the mold. The reason for this is that in the epoxy mold fabrication process, the male pattern is typically destroyed. A parting line surface is added, as shown below. Epoxy and glass cloth are layered around the male pattern to form the mold and are cured successively in layers. The figure below shows the beginning of the "lay up" process for the top half of the mold.
Curing of the mold epoxy can take from 0.5 to 40 hours. Aging the mold at room temperature increases the longevity of the mold. To structurally strengthen the mold and for fixturing, the epoxy lay up can be potted in a block of epoxy. After construction of the epoxy mold, steel inserts can be added for complex slides and coring and machining of the epoxy may need to be undertaken for example, in areas where sprues or gates could not be molded in.
Applications: Many of the molding methods can be combined to obtain greater flexibility in casting. Thus, dry sand cores often are used in green sand molds, and metal chills can be used in sand molds to accelerate local cooling. Ductile iron is widely used in the automotive and the related industries.The cast products are produced by using centrifugal casting technique.They are high purity alloys and exhibit stability in the microstructure with similar microstructural appearance.When compared with other static casting methods, higher values in the tensile strength, % elongation, hardness, wear resistance and fatigue strength are obtained with centrifugal casting techniques.
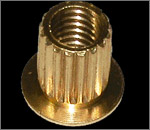
Cast products produced by the centrifugal casting technique using the composite mold consisting of ceramics and metal molds are inspected in order to observe the effect of centrifugal forces on the graphite particles present for discussing the changes observed in the graphite particle distribution, the hardness values and the microstructural formation in the direction from the outer to the center part of the cast product.
An apparatus and process for continuous horizontal casting of an ingot from molten metal. The apparatus comprises a mold for effecting rapid solidification of the molten metal into the ingot. A feed nozzle supplies the molten metal to the mold. Transition structure is disposed between the mold and the feed nozzle for solidifying the molten metal in the transition structure to prevent freeze back in the feed nozzle.