Introduction: Graphite mold casting technique is a modern affordable, quick and perfect casting methodology to produce graphite molds. Aluminum alloy and special zinc-aluminum alloys like ZA-12 can be best c
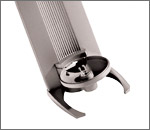
asted using this casting process. Graphite mold casting is a cheaper alternative to other casting methods which helps mass production of quality casting like camera housings.
Process: Graphite mold casting process is a simple process where a plastic aggregate consisting of graphite grains, pitch, carbonaceous cement, starch and water are use for making the mold. The mixture is squeezed around pattern and allowed to set. When the mold dried, it is fired to dry to form a strong mold. The mold is then assembled by fixing the sprue, cores and gates in its.
The two halves of the mold are locked together and molten metal injected into it under low pressure. Some foundries feed the molten metal into the mold from the bottom, using semi-automated machines. The mold is held together throughout the solidification stage of the casting. The mold halves are separated to remove the cast and the process is repeated again. When pouring care must be taken to to keep a control on the fill rate, cycle time, and temperature.
Graphite is said to be ideal for mold making because of its overall stability that holds their shape when filled with molten metal. Because graphite do not corrode, it has infinite shelf life. Graphite is a metal that is cheaper than tool steel. It requires no heat treating and its exceptional machinability dramatically improves the mold making phase.
Graphite Mold for Continuous Casting: Graphite mold is useful for continuous casting process. In a continuous casting process the pouring and solidification goes non-stops with the casted product being continuously withdrawn from the open end of the mold.
There are two types of continuous mold called the vertical (up-drawing) continuous casting and horizontal continuous casting. According to the materials used for the continuous casting process like the brass, red copper, aluminum, trey cast iron, the machine are names an brass continuous casting graphite mold, red copper continuous casting graphite mold, etc.
Applications: Railroad car wheels are cast in graphite mold accurately that requires no further machining. High-tech camera housings are perfectly casted using ZA-12 as alloy and graphite mold for the casting procedure.
Graphite molds for continuous casting: Graphite is widely used as a material for Continuous casting molds. Continuous casting is a casting method in which the steps of pouring, solidification and withdrawal (extraction) of the casting from an open end mold are carried out continuously. Graphite molds (dies) may be used
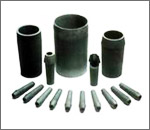
in both types of the process: vertical continuous casting and horizontal continuous casting. Most molds are fabricated from isostatically pressed graphite, however extruded graphite is also used for vertical casting of large ingots. Some alloys that are used for manufacturing continous casting in graphite molds re grey cast irons, white cast irons, aluminum bronzes, oxygen-free copper, etc.
Advantages of Graphite Mold Casting:
- Better dimensionally accurate castings are achieved at a much lower rate than in sand casting and investment casting
- The mold is inexpendable and does not warp or corrode, therefore it can be used repeatedly
- Graphite mold which is easily machinable can be created and modified quickly and economically.