Introduction: In
full mold casting instead of wood or wax thermally decomposable material like polystyrene is used for making pattern. A process similar to lost wax process, here the
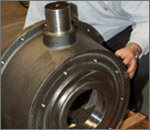
foam disappears when the molten metal is poured into the mold, therfore the process in expendable. The polystyrene pattern can be designed with the aid of a computer, that helps in making alteration to the design before the actual process is done.
Process: As in lost wax process, in
full mold casting, the pattern is made using a material that disappears in during the casting process. After coating the pattern with a refractory material it is used in a single piece sand mold. The advantage of the process is that complex molds can be cast without the use of draft. This process was first used in green sand molds.
Small volumes of patterns can be machined or hand made from a solid block of foam. For small volume runs the pattern can be hand cut or machined from a solid block of foam. For large volumes the pattern material can be injected in a preheated aluminum mold and steam is applied to it. Once the pattern is removed for the aluminum dies, gating systems and sprues can be hot glued into the pattern.
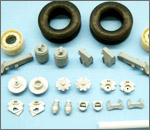
The pattern that is made of polystyrene is placed in the molding box and rammed to harden the sand. The mold is provided with sprues and gating in order to allow the molten metal to enter every cutting and intricate designs made by the pattern. Now, molten metal is poured on the polystyrene pattern. When the molten metal touches the pattern, it evaportes and takes the shape of the mold cavity.
Applications: Aluminum, iron, steels, nickel alloys, copper alloys can be cast in this method. Complex castings like pump housings, manifolds, and auto brake components are cast using
full mold casting method.
Advantages:
- This process is advantageous for complex castings that is usually done using cores and drafts
- It is an effective method for both small and large mold production
- A time saving and cost saving method, since the pattern need not be shaped as in wood patterns
- Patterns are not be stored unlike other casting techniques where metal, wood and plaster pattern are kept for future use.
- Pattern correction can be easily in the computer before the actual casting process begins
- Casting weight is reduced
- No draft allowance is required since foam is used
- Dimensionally accurate castings can be produced
- Simpler process and the foam is cheaper than wax.