Introduction: Also known as centrifugal rubber mold casting (CRMC), the main features of spin casting process is the use of rubber mold and employing centrifugal force for c
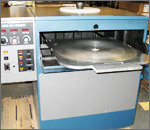
asting. During the solidification process the mold spins on it central axis till the metal solidifies in the mold. Spin casting is a widely used non-expendable process, for casting products that have excellent details and surface finish.
Process: For
spin casting, first strong patterns are made out of silicon rubber or investment cast wax, that are designed using rapid prototyping system or other pattern making methods. The pattern are places in a uncured silicon mold to create a casting mold. When the silicon mold is cured it is spun on its axis, and during the process the molten metal with low melting metals such as zinc, pewter, tin or lead are poured into the center of the mold. Centrifugal force pushes the charge through the runner. The mold spin when the metal solidifies.
Silicone or organic rubber is used is used for
spin casting, which is vulcanized to make a strong mold. Vulcanization is process used on rubber to make it elastic or to harden it. Before vulcanization the mold of rubber is soft, which can be easily cut and incorporated with the patterns. When vulcanized the mold becomes strong and rigid and a strong impression of the pattern is made in the mold cavity. The mold becomes strong when cures. The cured rubber mold can be used for repeated number of castings. Cores, inserts and other pull-out sections can be easily fitted into it which m
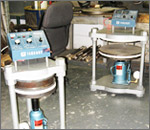
akes the process useful for complex castings. Since the rubber and silicon are soft initially, gate. runner system and air vents can also be cut into the mold effortlessly.
Applications: Spin casting is applicable for a wide variety of industrial, decorative, novel items, fashion accessories, etc. Plaster and metals with low melting poring and viscosities like pewter, zinc alloys, etc can be spin casted. Some of the products that are spin casted are inserts such as those used in fishing lure manufacturing, fishing tackle components, belt buckles, pins, emblems, medallions, trophies, assorted souvenirs etc. In addition, effective models of fragile rapid prototype models an be quickly made.
Advantage:
- Cast parts may be finished or painted as desires
- A quick casting process
- In a mold around 50 small to medium castings can be made in an hour
- Parts of any complexity can be handled
- High integrity, close tolerance parts with excellent surface finish are produced
- Low start up cost hence conducive for hobbyist and small business ventures.