Iron is one of the commonest (and cheapest) metallic elements on the planet. In fact, by weight it makes up about 5% of the planet's crust, where it is found as a range of slightly impure "iron ores": hematite, limonite, magnetite, etc.
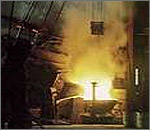
It was not until about 1200 BC that iron became general for the production of tools because the temperatures needed to process the ore exceeded what most ancient kilns were able to reach. Pure iron has a melting point of 1,535°C. The limit of an ancient furnace was about 1,150°C. (By contrast, copper has a melting point of 1,083°C, and ancient pottery kilns sometimes also reached temperatures in this range, but it was rare to get far above it.)
It was eventually discovered that the introduction of three to four percent carbon to the mixture could sometimes lower the melting temperature (ultimately to as low as about 1,150°, hence just at the furnace limit). Unfortunately, carbon also tended to contribute to the brittleness of the resultant products. Therefore the controlled introduction of carbon into iron ore remains a critical aspect of iron and steel production. (Carbon is not used in the production of bronze.)
Carbon was not the only technological innovation involved, however. Furnace structure and fuel were important in reaching the necessary temperatures. Hardwoods, such as those of the central African area, burn hotter than softer woods. (This is probably the reason for the especially widespread mastery of iron in some areas of Africa.) Further, the use of charcoal in place of wood allowed a yet hotter fire. So did the eventual discovery of coal as a fuel. Similarly, the use of bellows to force air into the kiln produced more rapid burning and faster release of heat by increasing the oxygen available to the fire.
Carbon-free iron heated to the maximum of ancient furnaces, while still not actually reaching its melting point, could be pounded (forged) to purify it and shape it, even without any admixture of carbon. Iron worked in this way and containing only negligible carbon is called "wrought iron," and its production is necessarily quite time-consuming. On the other hand, iron with high carbon content and as a result with a lower melting point could be melted and molded and is referred to as "cast iron." In Europe successful iron casting dates only to about the 1300s AD. However, in China iron casting dates to the 500s BC, when cast iron began to be used for the production of agricultural implements.
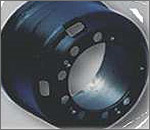
Even once the technology was known, manufacturing iron was not easy and could easily fail if the ore was not sufficiently porous or if there was too much oxygen available or if the lumps of charcoal usedto introduce carbon were too large.
The term "Iron Age" is given to those periods around the world in which iron came into general use. The specific dates of course vary from region to region, and the rigidity with which one defines "general use." One date sometimes given for the earliest iron production is about 2000 BC (for Turkey). Iron appeared in Africa by 600 BC, probably from Southwest Asia via Egypt, Nubia, and the Sahel corridor running south of the Sahara, and substantial iron working began in what is today Nigeria by the 300s. In most parts of the world, the use of iron largely displaced the prior use of bronze, and hence the "Iron Age" succeeded the "Bronze Age." Except in the northeast, there was no Bronze Age in Africa, where iron directly displaced the use of stone tools.