CNC stands for Computer Numerical Control and has been around since the early 1970s. Prior to this, it was called NC, for Numerical Control. (In the early 1970's computers were introduced to these controls, hence the name change.)
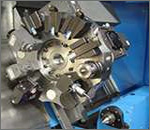
While people in most walks of life have never heard of this term, CNC has touched almost every form of manufacturing process in one way or another. If you'll be working in manufacturing, it's likely that you'll be dealing with CNC on a regular basis.
Before CNC: While there are exceptions to this statement, CNC machines typically replace (or work in conjunction with) some existing manufacturing process/es. Take one of the simplest manufacturing processes, drilling holes, for example.
A drill press can of course be used to machine holes. (It's likely that almost everyone has seen some form of drill press, even if you don't work in manufacturing.) A person can place a drill in the drill chuck that is secured in the spindle of the drill press. They can then (manually) select the desired speed for rotation (commonly by switching belt pulleys), and activate the spindle. Then they manually pull on the quill lever to drive the drill into the workpiece being machined.
As you can easily see, there is a lot of manual intervention required to use a drill press to drill holes. A person is required to do something almost every step along the way! While this manual intervention may be acceptable for manufacturing companies if but a small number of holes or workpieces must be machined, as quantities grow, so does the likelihood for fati
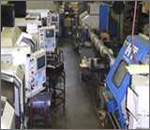
gue due to the tediousness of the operation. And do note that we've used one of the simplest machining operations (drilling) for our example. There are more complicated machining operations that would require a much higher skill level (and increase the potential for mistakes resulting in scrap workpieces) of the person running the conventional machine tool. (We commonly refer to the style of machine that CNC is replacing as the conventional machine.)
By comparison, the CNC equivalent for a drill press (possibly a CNC machining center or CNC drilling & tapping center) can be programmed to perform this operation in a much more automatic fashion. Everything that the drill press operator was doing manually will now be done by the CNC machine, including: placing the drill in the spindle, activating the spindle, positioning the workpiece under the drill, machining the hole, and turning off the spindle.
How CNC works: There is another article included in this web site called The Basics of CNC that explains how to program, setup, and operate CNC machines in greater detail. Additionally, we offer a series of products aimed at helping you learn how to use CNC machines. Here we're relating how CNC works in very general terms.
As one might already have guessed, everything that an operator would be required to do with conventional machine tools is programmable with CNC machines. Once the machine is setup and running, a CNC machine is quite simple to keep running.
In fact CNC operators tend to get quite bored during lengthy production runs because there is so little to do. With some CNC machines, even the workpiece loading process has been automated. (We don't mean to over-simplify here. CNC operators are commonly required to do other things related to the CNC operation like measuring workpieces and making adjustments to keep the CNC machine running good workpieces.)
Types of CNC machines: As stated, CNC has touched almost every facet of manufacturing. Many machining processes have been improved and enhanced through the use of CNC. Let's look at some of the specific fields and place the emphasis on the manufacturing processes enhanced by CNC machine usage.
In the metal removal industry: Machining processes that have traditionally been done on conventional machine tools that are possible (and in some cases improved) with CNC machining centers include all kinds of milling (face milling, contour milling, slot milling, etc.), drilling, tapping, reaming, boring, and counter boring.
In similar fashion, all kinds of turning operations like facing, boring, turning, grooving, knurling, and threading are done on CNC turning centers.
There are all kinds of special "off-shoots" of these two machine types including CNC milling machines, CNC drill and tap centers, and CNC lathes.
Grinding operations of all kinds like outside diameter (OD) grinding and internal diameter (ID) grinding are also being done on CNC grinders. CNC has even opened up a new technology when it comes to grinding. Contour grinding (grinding a contour in a similar fashion to turning), which was previously infeasible due to technology constraints is now possible (almost commonplace) with CNC grinders.
In the metal fabrication industry: In manufacturing terms, fabrication commonly refers to operations that are performed on relatively thin plates. Think of a metal filing cabinet. All of the primary components are made of steel sheets. These sheets are sheared to size, holes are punched in appropriate places, and the sheets are bent (formed) to their final shapes. Again, operations commonly described as fabrication operations include shearing, flame or plasma cutting, punching, laser cutting, forming, and welding. Truly, CNC is heavily involved in almost every facet of fabrication.
CNC back gages are commonly used with shearing machines to control the length of the plate being sheared. CNC lasers and CNC plasma cutters are also used to bring plates to their final shapes. CNC turret punch presses can hold a variety of punch-and-die combinations and punch holes in all shapes and sizes through plates. CNC press brakes are used to bend the plates into their final shapes.